We know, there’s no such thing as a stupid question. But there are some questions you might not want to ask your local shop or riding buddies. AASQ is our weekly series where we get to the bottom of your questions – serious or otherwise. Curious about something? Submit your own question.
Welcome back to the Bikerumor Ask A Stupid Question series. This week we’re talking about carbon fork design. The chances of a carbon fork actually breaking on you are extremely slim these days, and manufacturers go to great lengths with their modeling and quality control methods to ensure that is the case. Nonetheless, given some well-publicized historical cases of carbon fork failure, we’re aware that some riders still see this as an area of concern.
After receiving some poignant questions from one of our readers, and with the growth of integrated designs funneling brake hoses and shifting wires in and out of a steerer tube and fork leg, we thought we’d bring in some experts.
Two bike brands chimed in to discuss carbon fork design, and in particular, the possibility of a steerer/headset/stem interface redesign with full stealth cable routing in mind. Your experts are:
- Marcellus Putschli, Product Engineer at Bombtrack Bicycle Company
- Charlie Ward, Test Engineer at Scott-Sports

1. Would it be possible to design a headset and carbon steerer system that doesn’t use a compression ring and otherwise minimizes damage from over-compression by those who don’t use torque wrenches (surprisingly many of them), stems without a full-coverage clamping surface, grinding away by internally routed brake/shift hoses and cable housings, and cumulative minor impact forces to the steerer (riding over railroad tracks, potholes etc.) which can weaken it over time.
Scott: It could be possible. There are many aspects of design yet to be explored and many that have already been used to good effect in the history of bicycles. As we see it, this is currently the best assembly method to ensure efficient steering, rider safety, and compatibility of parts.
Any mechanical joint, and especially those that use bearings, are sensitive to assembly torque, and therefore preload on the bearings. It is really unavoidable for a lightweight structure like a bike to be designed to sustain unknown assembly torques. The other aspects you mention are all considered in the engineering phase of our developments, and we follow the international standards and have created our own standards to make sure our bikes stand the test of time.
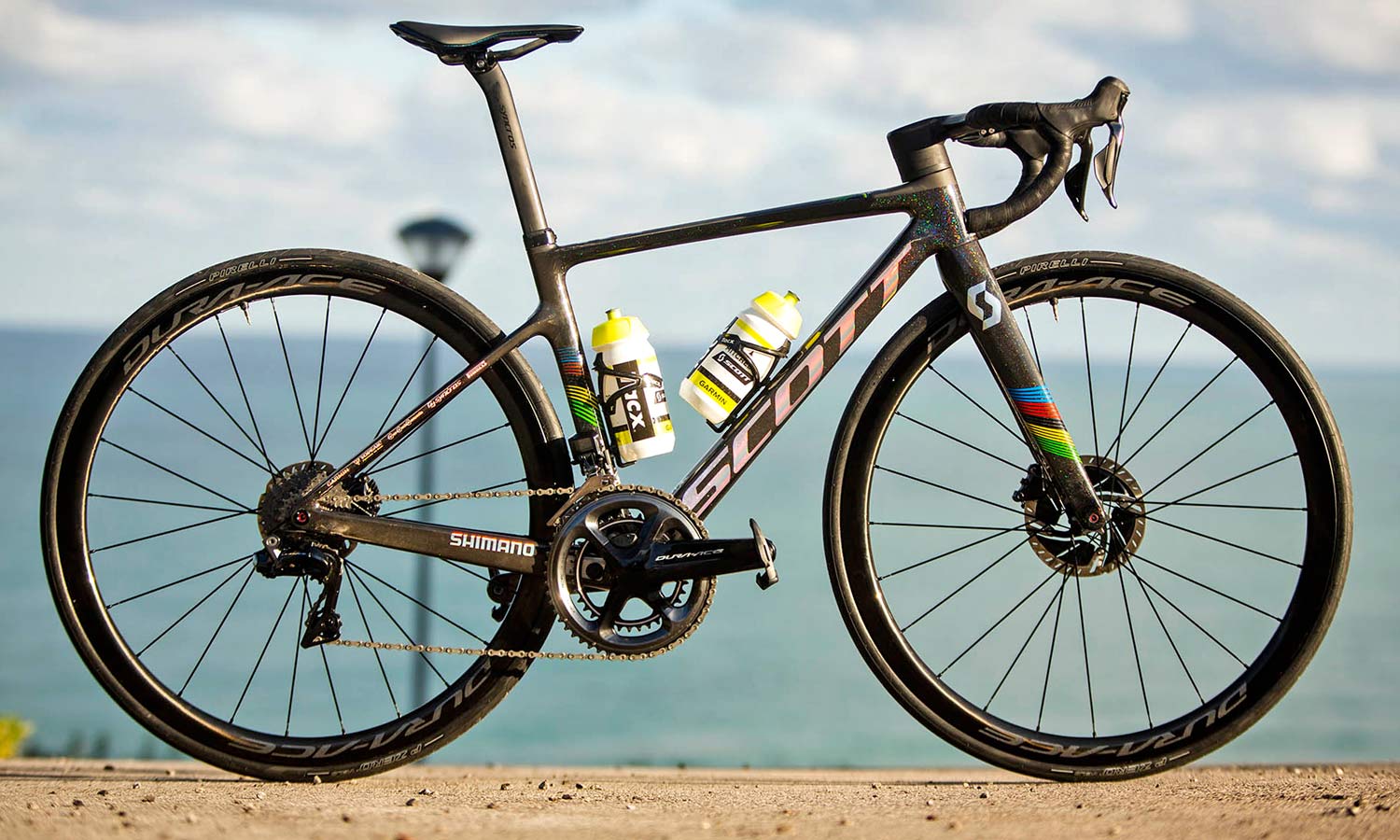
Bombtrack: This is a hard to answer question, as it already implies a certain direction to the solution of the problem of carbon steerer breakage. I would rather, ask if we need to reduce safety margins for low weight, or offer a very labor and QC-intense product for a low price point before introducing a new stem/headset/steerer interface into the bicycle world that is not short of various competing standards.
But to answer this question: Yes, of course it would be possible to design a completely different system. The current headset/stem interface was developed with aluminium or steel steerers and stems in mind. It is not optimized for the use of fiber-reinforced materials, as the force applied hits the fibers orthogonally. So, developing a new interface would offer a lot of benefits, but it will come at a cost.
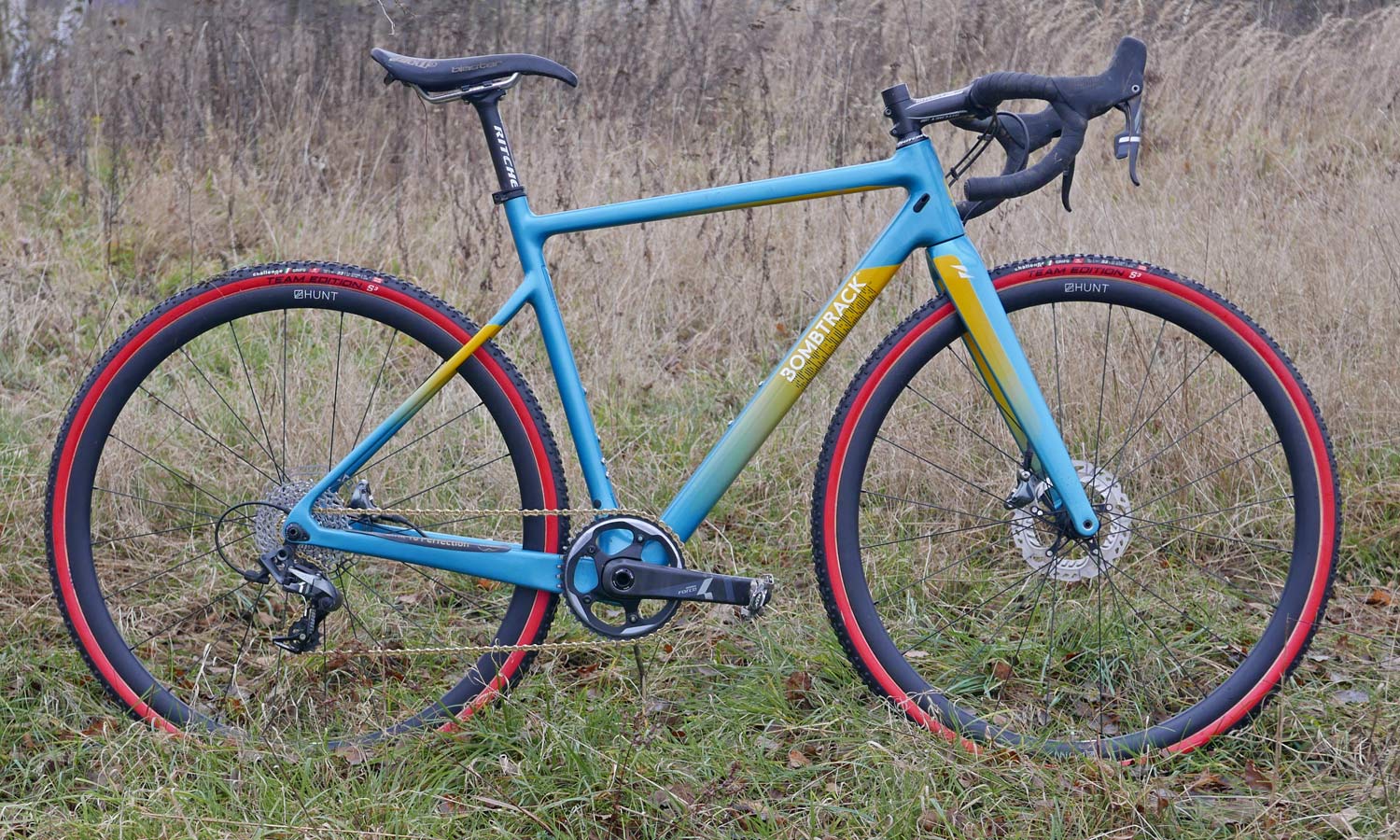
To be really suitable for the use of composite materials it won’t be backwards compatible with the current stem/headset/steerer interface. This will also mean that various manufacturers will have to work together, so that headsets/stems and forks are available at the same time, otherwise such a system won’t be accepted by the market. In the end, I am not convinced that the benefits will justify the introduction of such a new standard.
However, I don’t think we need to go that route right now. A lot can be done to make the current interface safe, even by the consumer after purchasing a bike (of course, first of all those things should be done during production). Deburred edges, correct internal cable routing, friction paste for carbon stems, a sufficiently long expander, correct amount of headset spacers, and the use of a torque wrench should be self-evident for production, shops, and home mechanics.
Sufficient safety margins and proper quality control need to be implemented by the manufacturers. Of course both will come at a cost: Bigger safety margins result in extra weight, and higher-level quality control adds cost that trickles down to the retail price. Unfortunately, both these factors shrink the viability of a product, especially that of carbon parts since they are already expensive and offer great potential for weight savings.
Also, carbon parts need to be professionally inspected or replaced after a crash (sorry, this also includes the random tip over at a coffee stop). A properly designed and maintained fork won’t suffer from cumulative minor impact forces, at least not during the normal lifespan of a bike.
2. Why don’t manufacturers bond or in-mold a thin metal sleeve over the carbon steerer where the compression ring, stem, and bearings contact it, to strengthen the steerer and improve its longevity?
Bombtrack: This is a method that would add cost, complexity, and weight to the production of a fork while reducing the outer steerer diameter (the part of the steerer that is most relevant for stiffness). It is not necessarily a bad method, as it helps to distribute the load, but again it will come at a cost.
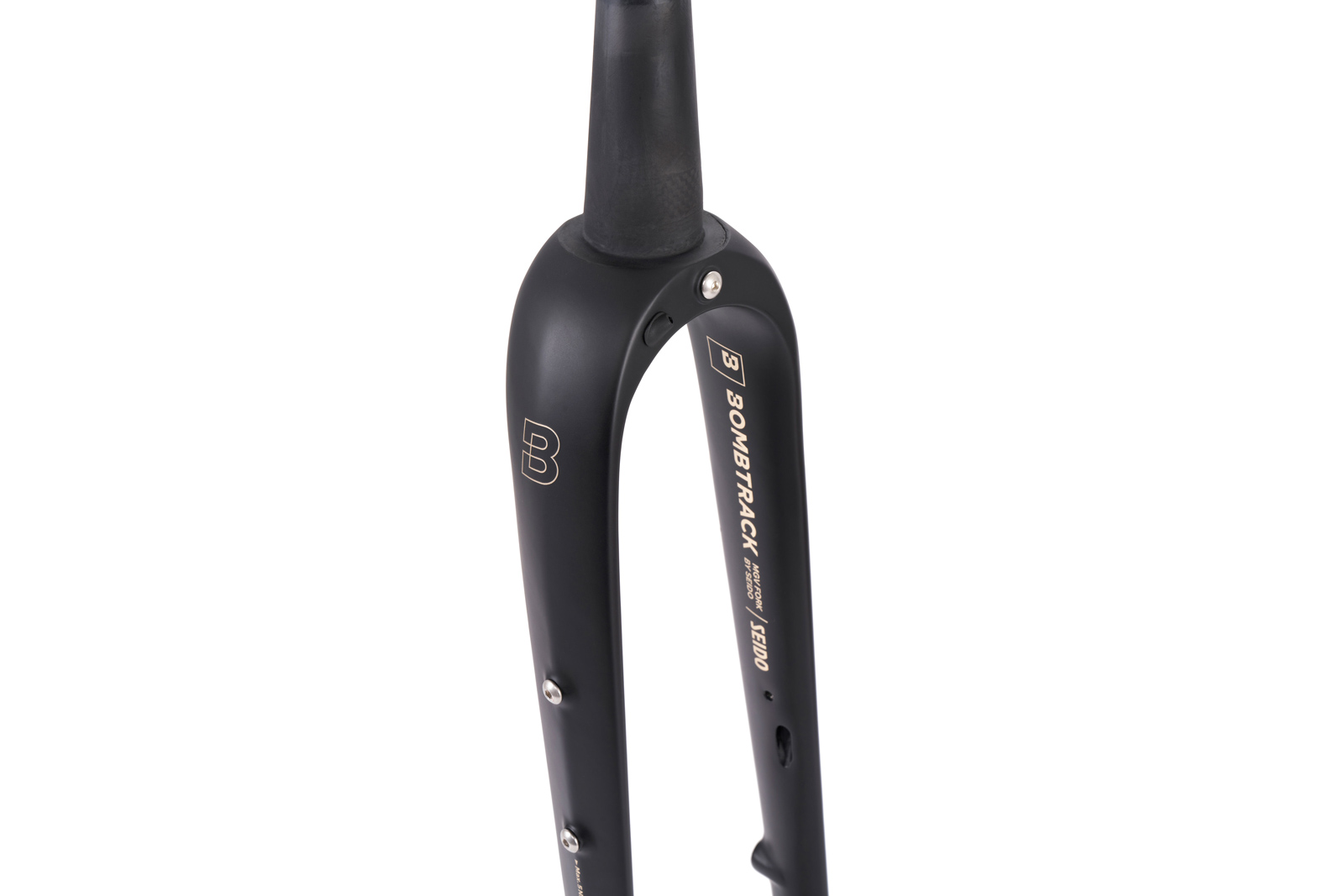
Personally, I would rather optimize the other parts of the system than reduce the wall thickness of the steerer in the area of its maximum load. Also, most carbon forks will come with a set steerer length that gets cut down to its correct length during the assembly of the bike. This means a metal sleeve needs to be long enough for all possible headtube lengths, so it will be much longer than necessary on a taller frame. All things considered, it seems that this solution works rather as a patch than tackling the root cause of the problem.
Scott: We do use inserts already in the dropouts or brake mounts for example, but in those cases, they can be fully enclosed in carbon with the fibers running around both sides of the part. In-molding metal sleeves in a steerer tube is very difficult to do in a way that improves the resistance to wear without drastically reducing the strength.
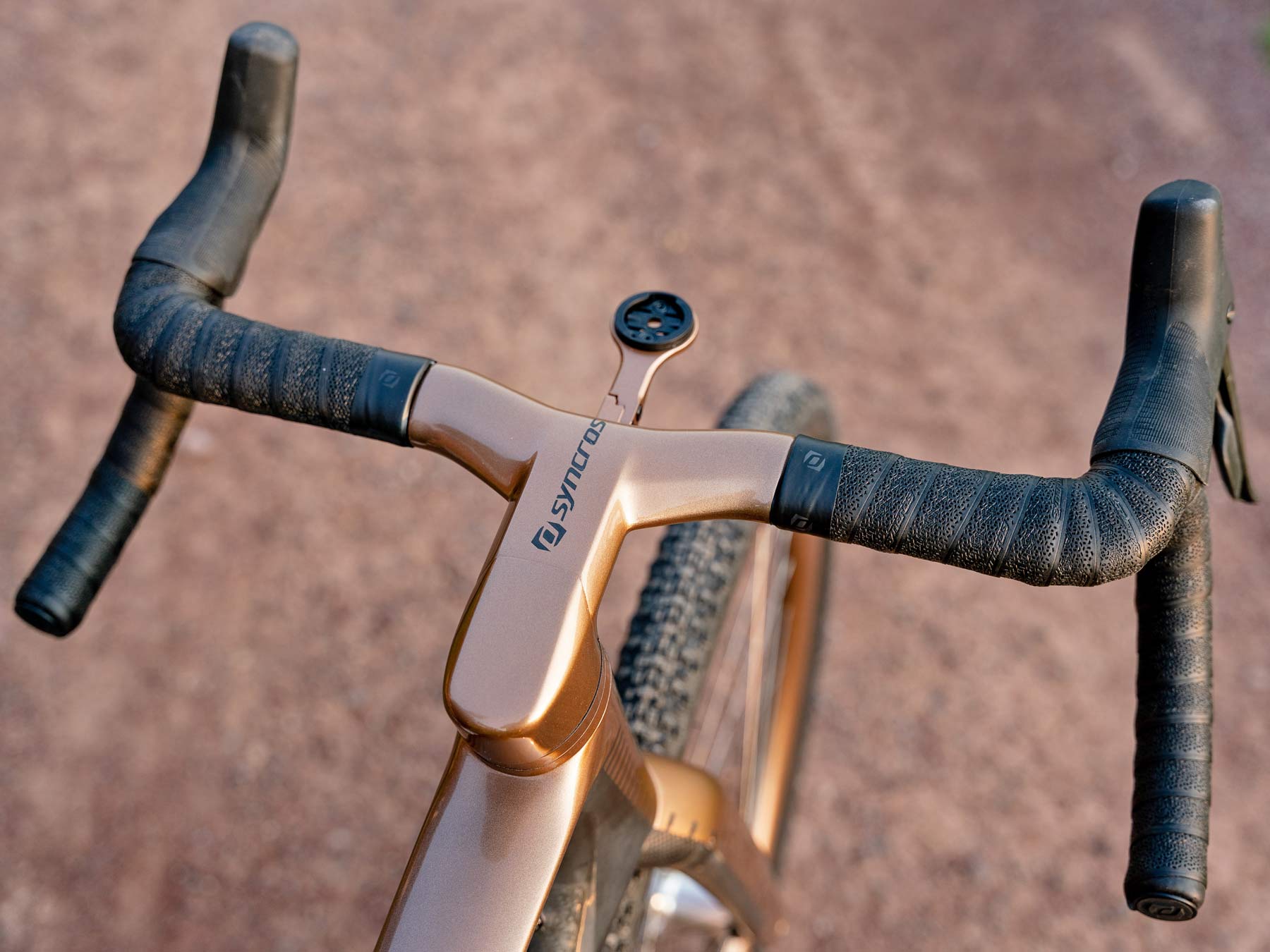
A sleeve on the outside of a steerer would mean that the carbon fibres would have to either be cut to insert the sleeve, or molded around the sleeve, both of which would reduce the strength of the steerer. If we consider the transmission of forces into the steerer, then reducing the number of parts in between actually improves the situation; having a direct connection between the carbon bar/stem combo and the steerer tube gives the best possible stress distribution. Adding a metal-to-metal contact between the sleeve and the bearing could also introduce the danger of corrosion and frictional effects such as fretting.
3. Why don’t manufacturers check every fork with a scanner to test for voids and other defects you can’t see (as far as I know Canyon Bikes does this)?
Scott: CT scanning is a great method to identify flaws in carbon structures. The machines that are available now are really impressive, but also limited in terms of what they can achieve on a mass production scale. If you really want to get a detailed scan and see defects in the structure on a sub-millimetre scale over a whole fork, for example, each fork needs a long time in the machine resulting in a huge amount of data that needs to be processed, analyzed, and stored.
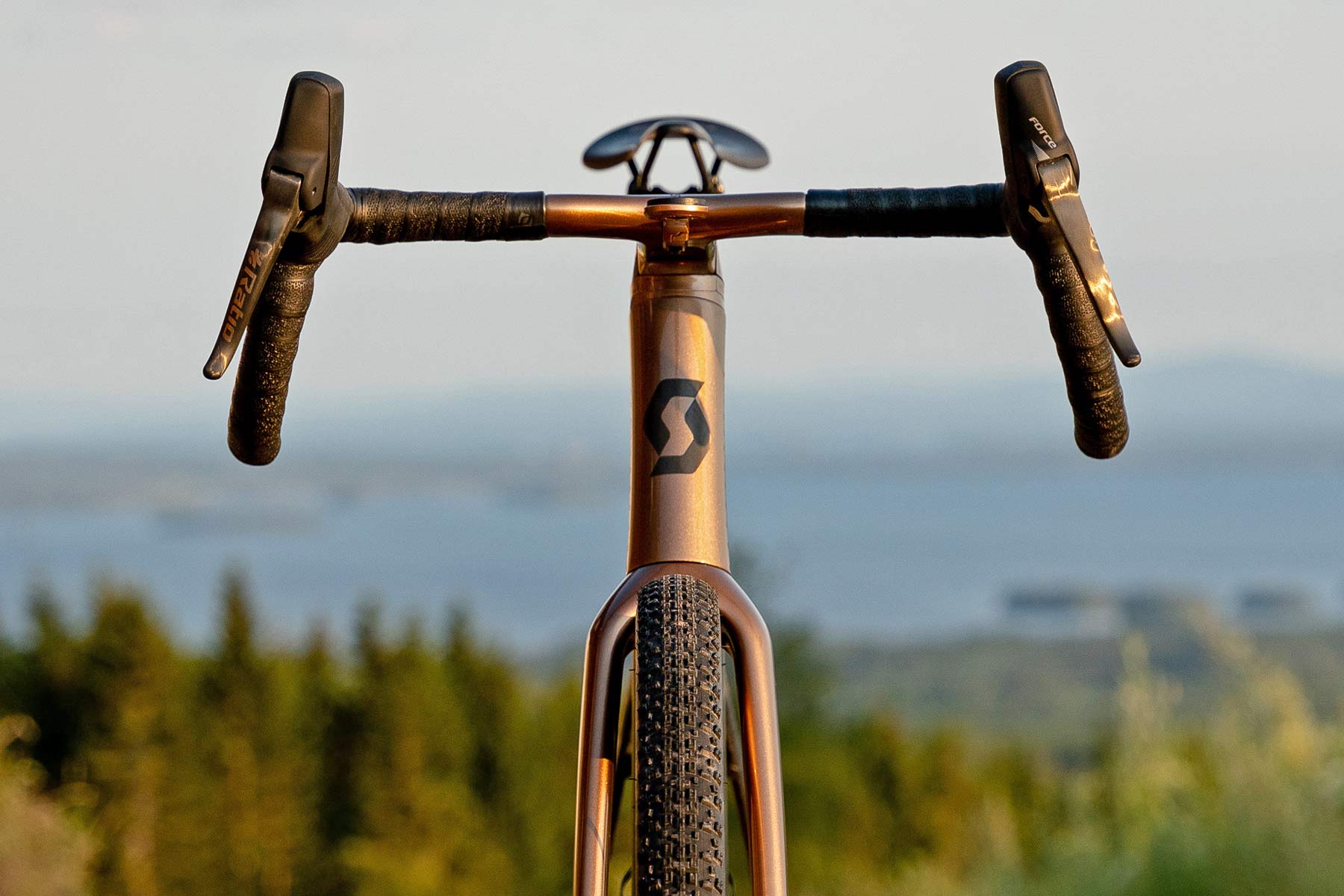
This requires some substantial computing power and staffing which at the current point is not possible to implement without a significant price increase for the end product. It is an invaluable system that we regularly use in development and research, but we have a high level of confidence in our production methods and QC, so the chances of having critical defects in an end product are kept to an absolute minimum.
Bombtrack: Quality control is important, but it doesn’t help against design flaws, so unfortunately a scanner won’t guarantee that a part doesn’t break. With that said, there are various methods of ensuring proper quality during the manufacturing process, for example keeping track of the weight of the used materials, measuring the stiffness of the product, checking the geometry, doing x-rays, tap tests, and ultrasonic scans as well as CT and thermographic scans. All of those methods are non-destructive and can be used during various stages of manufacturing.
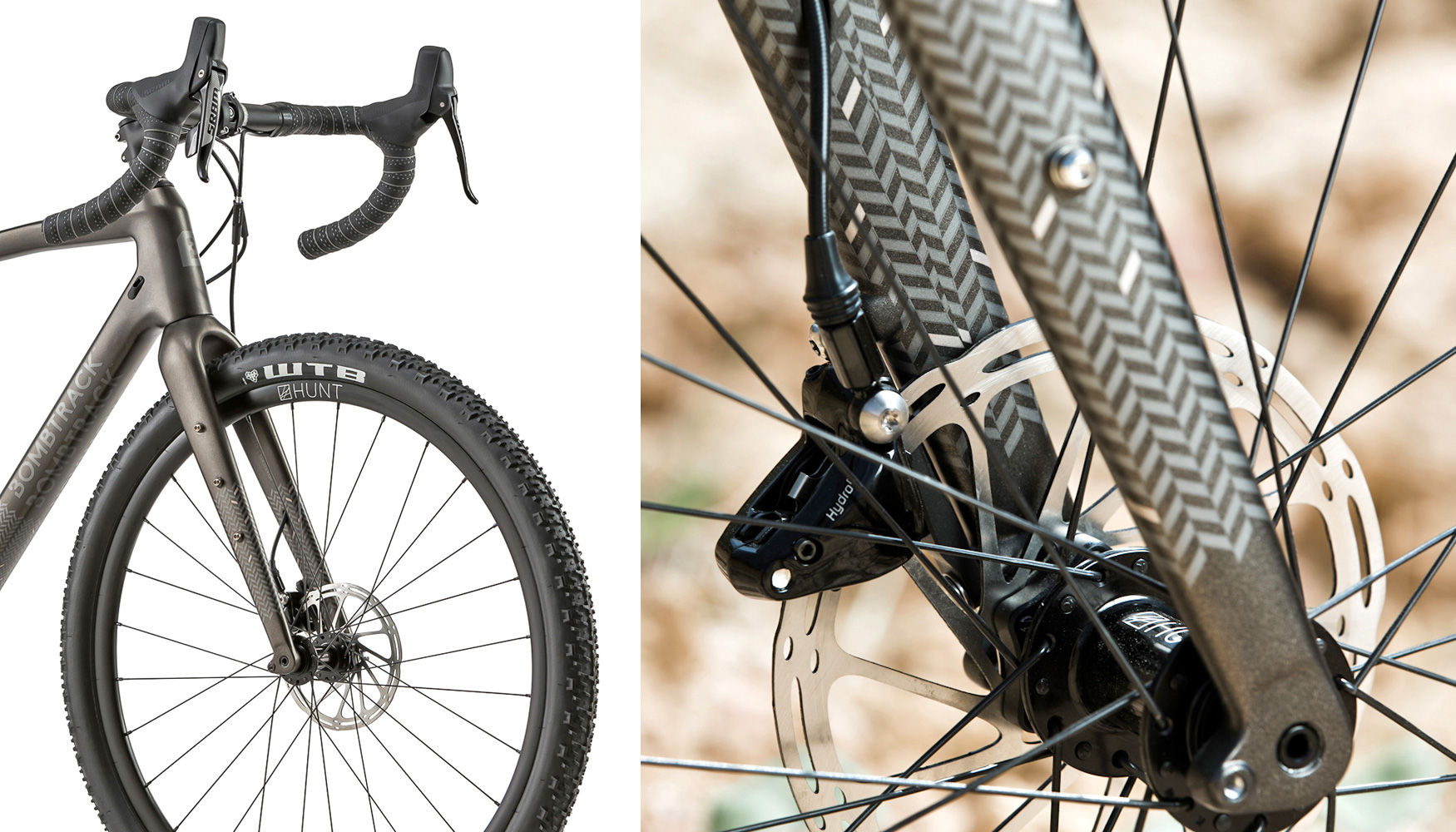
Another important aspect is the skill level of the workers, the quality of the tooling, the quality of the resin, storage of the raw material, and air temperature and humidity in the factory as well as following the exact layup plan.
All of the described methods have their pros and cons, and while a CT scanner is a very impressive machine, it only helps to spot mistakes already made. Designing material-specific, adding sufficient safety margins, and investing in a skilled and consistent labor force while keeping close track of all manufacturing steps helped us to avoid any major fork defects. In addition, we do a third-party quality control and regular destructive tests. So far, we haven’t had any fork or frame recalls.
4. What else can be done to re-design the carbon steerer-headset system so we can all ride carbon forks safely for years, in real-world conditions? I would gladly add 100-150 grams for a stronger and more durable carbon fork I know I can depend on for years. And I think most of us would. Thanks!
Bombtrack: The answer lies within the question. There is no free lunch, if you want a safe carbon fork don’t shop for the lightest fork and especially not for the lightest compression cap. If you really need to have a very lightweight fork then be prepared to pay the price. Not only the purchase price but also the cost for proper tools, a good mechanic, and the replacement or scan in the case of an accident. If you want to have a worry-free fork that can take a beating then maybe a steel or aluminum fork fits your needs better than a carbon one. Don’t forget, weight is not everything.
With that said, I think getting rid of the expander and increasing the contact area of the stem will both have the biggest potential to increase the durability of the stem/steerer interface. There are already several systems available that don’t rely on the expander to adjust the correct headset play. And, when most riders add spacers underneath the stem while having to add a 5mm spacer above the stem as well, it would make much more sense to integrate those spacers into the stem and increase the clamping area by 15mm or 20mm.
Scott: SCOTT is very proud to still have many of our older models still out in the market and rolling without issues many years on. I’d still emphasize here: real-world conditions are very difficult to predict. We always consider what we call ‘foreseen-misuse’ in our engineering and design, and it is one of the reasons that mass production carbon bikes can’t be as light as some boutique brands. One person’s gravel is another person’s XC, but SCOTT strives to be very clear with what each of our bikes are built to withstand and make sure our test standards consider the harshest use cases.

Got a question of your own? Click here to use the Ask A Stupid Question form to submit questions on any cycling-related topic of your choice, and we’ll get the experts to answer them for you!